National Car Transport Company
Supply Chain Tracking and Consolodation


This client stands as a distinguished entity in Australia's finished vehicle logistics landscape. They provide an end-to-end supply chain solution that seamlessly spans from the arrival of vehicles at the port to their final delivery, encompassing a broad spectrum of transportation needs.
Here's an overview of what they offer:
Vehicle Transportation: This client extends comprehensive vehicle transport solutions throughout Australia, tailored to meet the diverse needs of their clientele:
- For Bulk Fleet Movements: They are the go-to for leading vehicle manufacturers, importers, and dealerships, ensuring large fleets are moved with precision and care.
- For Individual Vehicle Deliveries: Their customized services are designed to accommodate the specific requirements of companies, small businesses, and private owners.
- For a Range of Vehicle Types: The transport services are adept at handling passenger cars, light and heavy commercial vehicles, ensuring every vehicle is delivered with the utmost attention.
Integrated Logistics for the Automotive Sector: a pivotal link for top-tier automotive stakeholders worldwide, providing integral support to:
- Vehicle Manufacturers
- Importers
- Fleet Operators
- Dealerships
- Individual Customers:
- They also extend their expertise to the general public, offering a suite of services catered to individual needs.
The implementation of the RFID-based solution by Clevvi revolutionized the clients Services' operational efficiency and accuracy in vehicle logistics. The immediate impact was a dramatic reduction in vehicle allocation and delivery times, directly translating into a more dynamic and responsive supply chain.
This enhanced efficiency not only improved the company's capacity to handle higher volumes of vehicle movements but also significantly reduced the likelihood of delivery errors, ensuring that vehicles reached their intended destinations as planned.
Moreover, the increased visibility and real-time tracking facilitated by the RFID system empowered Autocare Services with unprecedented control over their logistics operations, enabling better decision-making and resource allocation. The result was not just an uplift in operational performance but also a notable improvement in customer satisfaction levels. Dealerships benefitted from more reliable and timely vehicle deliveries, reinforcing their trust in their Services. This strategic technological enhancement fortified the clients Services' reputation as a leader in the vehicle logistics sector, setting a benchmark for innovation and efficiency in the industry.


The company’s legacy system was rigid, and faced a significant logistical challenge with their old system for allocating vehicles off the docks to the network of trucks responsible for delivering them to dealerships across Australia. The existing system, steeped in legacy processes, was not only time-consuming but also prone to errors due to its heavy reliance on manual intervention. The allocation process was complex, needing to account for various factors such as delivery schedules, truck capacities, and specific dealership requirements.
The inefficiencies were multifold. Firstly, the old system struggled to provide real-time visibility of vehicle status, leading to delays in transportation and, consequently, dealership stock shortages or surpluses.
Secondly, the inability to quickly adapt to changes in delivery demands often resulted in sub-optimal routing of trucks, increasing transit times and fuel costs. Furthermore, the manual system lacked the flexibility to efficiently handle the variability in vehicle types—from passenger cars to heavy commercial vehicles—which often led to underutilized truck space or the need for additional trips.
These challenges were not just operational but also impacted customer satisfaction. Dealerships were at the mercy of estimated delivery times, which, when not met, strained relationships and tarnished their Services’ reputation for reliability. This old system was clearly a bottleneck in their otherwise streamlined supply chain, calling for a modern solution that could match the pace and scale of their nationwide operations.
Clevvi addressed this clients logistical challenge through the innovative use of RFID (Radio-Frequency Identification) technology, tailored specifically to streamline the vehicle allocation and delivery process from docks to dealerships across Australia. This solution was centered around linking each vehicle's unique VIN (Vehicle Identification Number) to an RFID tag, enabling a transformative leap in efficiency and accuracy for the entire distribution network.
The implementation of RFID sensors at critical junctures—starting from the docks—allowed for the instant identification of vehicles as they were offloaded. Drivers tasked with vehicle pickups were equipped with RFID readers, enabling them to quickly and accurately identify and confirm the vehicles assigned to their trucks. This system not only expedited the allocation process but also significantly reduced the margin for error, ensuring that the right vehicle reached the intended truck for its journey to the dealership.
Upon arrival at the dealerships, the same RFID technology facilitated a seamless confirmation process. The quick scan of the vehicle's RFID tag provided immediate verification of delivery, closing the loop on the vehicle's journey from dock to dealership. This not only streamlined the delivery process but also provided a real-time audit trail for Autocare Services, enhancing visibility and control over their nationwide logistics operations.
Clevvi's approach was simple yet profoundly effective, addressing the core issues of visibility, efficiency, and accuracy that had plagued their Services' old system. By leveraging RFID technology in such a targeted manner, Clevvi not only solved the immediate logistical challenges but also positioned their Services at the forefront of innovation in the vehicle logistics sector. This solution underscored the power of integrating digital technology with traditional logistics, setting a new standard for operational excellence in the industry.
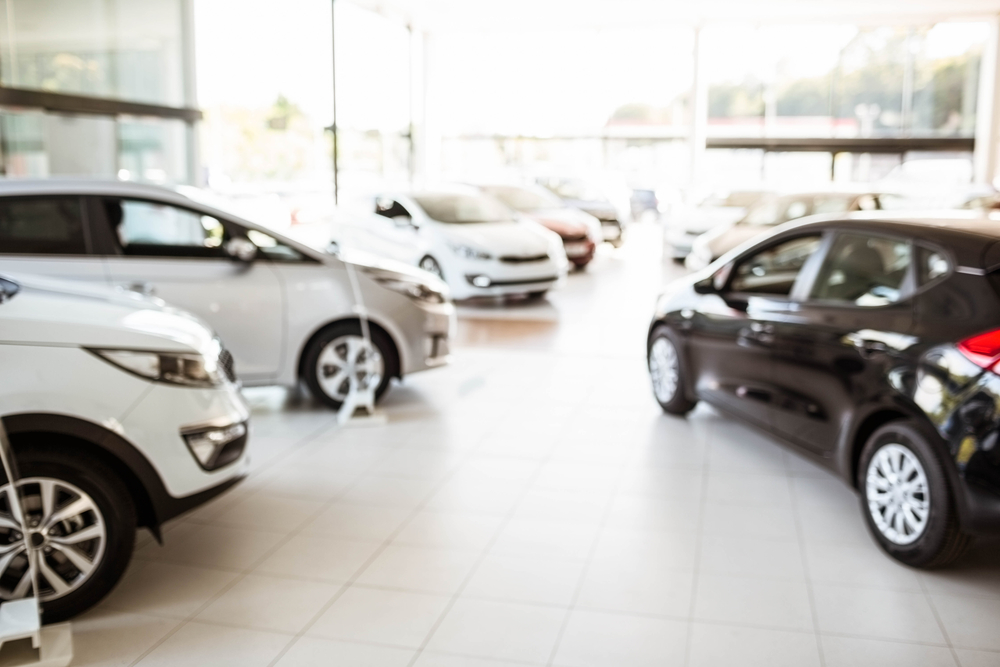
Clevvi are experienced in supply chain management, logistics, business process modernisation and innovative technologies to solve long standing company bottlenecks
Trusted by 200+ Australia/New Zealand Customers
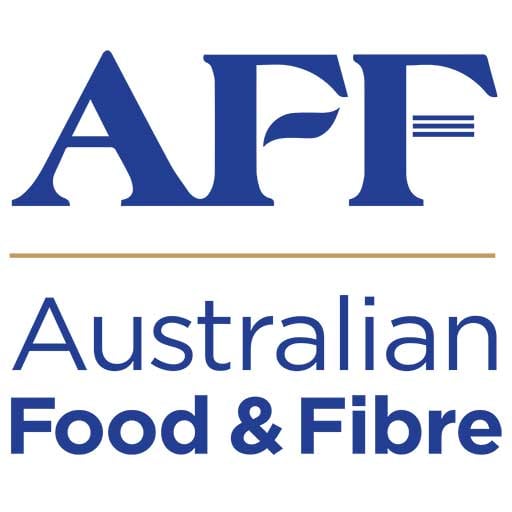
Australian Food and Fibre
AgricultureClevvi accessed real time ERP system data and overlaid this information on a device camera feed to a phone or tablet. The solution uses AR which shows product, weight and expiry in tubs using unique QR “license plates” instantly visually highlights expired product. The technologies included QR codes, computer vision/AR, Bluetooth/UWB, and data integration.
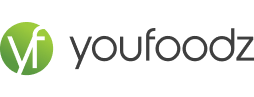
YouFoodz
Food Production
Transforming a complex, Excel-based model into a user-friendly web and mobile application that can cater to a userbase with wide-ranging computer literacy and allows continuous updates and easy maintenance by SRA staff.
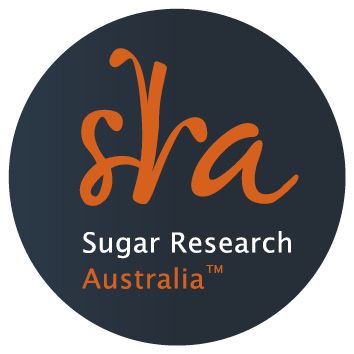
Sugar Research Australia
AgricultureThe challenge to collect data from existing factory equipment, send to the cloud and also to structure and interpret the collected data to provide an easy-to-read, insightful and actionable visualisation, and identify the correct data points to enable remote equipment performance monitoring and cost-efficient to run and maintain.
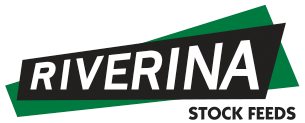